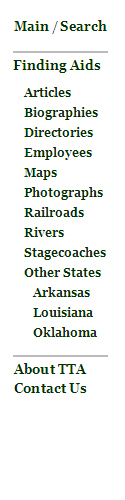 |
A Visit to the Kirby Mills (Gulf Coast Lumberman, 1937) |
|
|
|
|
|
Source: "A Visit to the Kirby Mills", Gulf Coast Lumberman, September 1, 1937. Bound in a scrapbook in the collection of Lester Haines. |
|
|
|
|
|
A Visit to the Kirby Mills |
|
|
The lumber industry has been asking and answering the question for more than a generation, "Is it as Good as Kirby's?" Because the name of Kirby in the lumber business has been since the opening of this century really a name to conjure with. The story of the formation of the great timber and milling empire established by John Henry Kirby in East Texas has often been told in these columns in years gone by. Once as many as fourteen big mills carried the Kirby banner in East Texas, and transformed those mighty East Texas pine and hardwood forests into quality building materials.
Today the Kirby group of actively operating sawmill plants numbers five, located at central points in the still great Kirby stand of timber Voth, Silsbee, Bessmay, Honey Island, and Call, Texas. They are splendid mills that represent all the intelligence and ingenuity in lumber manufacture that thirty-odd years of continuous large-scale operation have brought to the management.
Believing in the modern adage that he who stands still is in reality going backward, the Kirby organization has been quick-stepping for years past in the modernization of their mills, their equipment, and their methods of producing and preparing their goods for market. Today, at the Kirby group of mills, progress is the purpose, and they are going places. With a mill operating personnel that is ambitious to the nth degree and up on their toes every hour of the day and every day of the week, the visitor to the Kirby mill group immediately is impressed with the punchfulness he sees all about him.
Voth
Let's just take a little trip around these Kirby mills. Leave Beaumont early in the morning because you've got a big day ahead of you, and drive north on Highway 59. About nine miles from Beaumont you enter Voth, and there begins the Kirby lumber realm.
A typical sawmill town with its uniformly built houses, its general store, and office building . . . that's the first impression you get of Voth. But, if you have time, look around. You'll see that you are sadly mistaken if you think Voth is "just another sawmill town."
Located in the heart of a vast area of Texas timberland, the Voth plant was built in 1923-a mill with new ideas.
For instance, at Voth a brand new log carriage, made up of several parallel endless chains, moves logs from the logging trains to the mill. This speeds up the unloading operations, is less expensive, and requires less upkeep than the former, and now discarded, derrick method of unloading.
F. L. Roberts, mill manager at Voth, and incidentally a mill man from "way back," is as proud of this new part of the Voth mill as you were of your first watch. He says the chains have been in operation a little less than a month, and are running just like clock work.
Another idea not quite as new, but just as interesting, is the use of steam cranes for loading and unloading lumber. Running on the standard gauge railroad track, these huge monsters of steel pick up ten- to fifteen-ton piles of lumber just as if they were toothpicks. The cranes move the lumber anywhere . . . from the mill to the kiln cars from the cars to the piles for air drying . . . from the drying yard to the planing mill or the loading dock.
The bulk of Voth's lumber goes rough to leading manufacturers of furniture and other lumber consumers. Hence, the cranes save Kirby thousands of dollars annually. They believe them to be the cheapest, most efficient method of moving lumber in bulk.
The mill proper has two band saws and a resaw. Five dry-kilns properly condition the lumber, and right now Voth is operating on an eight-hour shift, producing 10,000 feet of lumber per hour. About 235 men are employed in the mill.
One of the most unusual things about Voth is the air drying yard where hardwood is stacked. The steam cranes make it possible to stack lumber to enormous heights, so that looking down on one of the "streets" of the yard, is just like beholding a deserted city street walled by skyscrapers. The cranes carefully stack the lumber on concrete and steel foundations that are elevated to permit the proper drying of the bottom pieces in the stack. The reason for high stacking is obvious saves space. Even so, the drying yard at Voth covers over 27 acres.
Lumber at Voth is air-dried for periods varying from four months to four years, depending upon the species and the purposes for which the wood will be used. Gum and magnolia are dipped in a chemical which acts as a stain preventive. Both Lignasan and Dowicide are used in the treatment of Kirby lumber.
Silsbee
Going north on Highway 59, some 11 miles, you come to Silsbee. The same air of progress, improvement, and modernity which prevailed at Voth is found at Silsbee, too. |
|
|
|
|
|
|
|
|
Silsbee is really the center for all of Kirby's mill operations. There are located: the general offices of the logging department; headquarters for Kirby's seven stores; maintenance shops for the machinery of all Kirby's big mills; round-house, where Kirby's many locomotives are kept in running condition; repair department for the six powerful steam cranes; railroad car shed, under which the hundreds of logging cars are assembled and kept in repair; and a big sawmill.
The Silsbee mill cuts only pine, producing approximately 2,225,000 feet monthly. A single band mill and bull edger do all the cutting. The large bull edger takes eight-inch cants without even a grunt! All the lumber is kiln-dried and the timbers are all lignasan-dipped, air-dried. Silsbee's new dry-kilns are made entirely of brick, concrete, and steel, and have just been completed. They were installed by The Moore Dry Kiln Company.
Most positive indication of progress at Silsbee is the construction of two new fire-proof steel sheds which make it possible for lumber to move from the kilns to the storage sheds, without ever being uncovered.
Larger of the two buildings is the cooling shed, built at the exit of the five Moore double-track kilns. The cooling shed runs 160 feet the entire length of the kiln exits, and is 64 feet in width. A roofed electric carriage moves the cars of kiln-dried lumber down to the end of the cooling shed to a track that extends some 100 feet to the take-down shed. This new, all-steel take-down and grading shed is 54 feet wide, and 210 feet long. Both of these new structures have just been completed.
Then, take the storage sheds. Patented Lamella roofing, a roofing idea which eliminates any sort of center support, has been installed, and the new sheds increase the storage capacity at Silsbee so that every piece of lumber on the plant is under cover.
W. A. Brownlee, a seasoned lumberman, is in charge of the mill operations at Silsbee. Mr. Brownlee has been with Kirby for 10 years, and had previously spent much time in Louisiana and Central America, where he learned Lumber.
The machine shop is another large and important department at Silsbee, and another new building. Built in 1935, the shop employs 61 men, working day and night to keep all the machinery in tip-top condition.
The shop is equipped with every type of modern metal-working machinery, from an electric hack saw to a gigantic forging machine. Master Mechanic Fred B. Hudgens says that there is no job too tough for the machine shop, with all its modern equipment, and its expert machinists.
The roundhouse, where Kirby's locomotives are kept in condition is also in line with the general atmosphere of modernity. Unlike other round-houses, it is clean and newly painted, and the yards are kept spotlessly clean in fact so clean that it doesn't really look like a round-house at all!
In charge of the company stores is H. C. Hopkins. The seven company-owned stores are located at Silsbee, Voth, Honey Island, Spunger, Bessmay, and Call, Texas; and Merryville, Louisiana. Mr. Hopkins said that a customer can buy anything at a Kirby store from shoe strings to porch swings.
Another department of the Kirby operations which is headquartered at Silsbee, is the logging operations. C. L. Young has charge of logging for all the mills. He is ably assisted by J. B. Gunter. These men, in addition to the usual duties connected with logging operations, see to it that suitable timber is furnished each mill. They personally supervise all special orders. Right now there are three logging camps furnishing Kirby's mills with timber: Merryville, Louisiana; Honey Island, Texas, and Camp Eleven, in Tyler County, Texas.
All the camps cut both pine and hardwood. The logs are brought from eight to thirty miles from the various logging camps to the mill, via Kirby's logging railroad, the Santa Fe Railroad, and by truck. Steam skidders and caterpillar tractors are used to get the logs from the woods to point of transportation.
|
|
|
|
|
|
Bessmay
Traveling still further north on Highway No. 59, we come to Kirby's greatest operation the Bessmay mill.
The huge mill with its ten smoke stacks belching forth grey smoke . . . its immense red metal burner emblazoned with the words "Kirby Lumber Corporation, Bessmay, Texas" painted in white letters over seven feet high . . . the endless trains loaded to capacity with pine logs and on the ground as far as the eye can see along the track, logs already unloaded all make the approach to Bessmay one of the most impressive views you will see in the sawmill country and one that is not easily forgotten.
Genial mill manager D. R. Bird is proud of the new improvements at Bessmay, just as all the other mill managers are at Kirby's other operations. In fact one of the first new things you will see at Bessmay will be Mr. Bird's new desk. The boys at the mill made it out of beautifully grained gum (Kirby cut and Kirby cured, of course) and put Mr. Bird's name-plate on it.
The mill is equipped with two bands, one horizontal resaw, and bull edger. It has two new brick kilns, which increase the battery of kilns to eight, double-tracked. Sprinkler systems, iron floor, brick walls, concrete roofing almost eliminate the fire hazard.
The planing mill is equipped with high speed steam driven equipment, and can put out 7,500,000 feet of planed lumber every thirty days, and as for storage a total of 14 large sheds is needed to hold Kirby's stock, their maximum capacity being 12,000,000 feet. Right now they have in stock about 7,000,000 feet, on which the turnover is very rapid. Manager Bird, talking about these sheds, said, "This is the finest set of sheds in the South." Another veteran in the lumber industry, Mr. Bird got his start as water boy in the woods, and has held every job in the milling end of the game, but he says he hasn't thoroughly learned sawmilling yet.
Right now 12 boilers are going full blast to generate steam for the big steam drive for the mill. But, manpower that will astound you is exhibited in one comparatively small department of the mill. In a corner of the planing mill, six men with hammers, and with right arms like steel, nail together 900 grain doors for railroad cars every day, in season.
Another idea now being put into operation at Bessmay to conserve steam, and increase power is a 1,000 horsepower turbo-electric generator. It is now at Bessmay, awaiting installation. It will concentrate the electric power at Bessmay into one unit, doing away with a number of small engines and long steam lines. This is the newest improvement at Bessmay and is expected to prove the most profitable.
On up the line is Kirby's other large hardwood mill, at Call, Texas. This mill has been in operation since 1925, and cuts something like 125,000 feet of hardwood in a 10-hour day. It is constructed of wood and steel.
Also at this point is located Kirby's oak flooring factory, which produces Kirby brand oak flooring. This plant is under the direct supervision of J. M. Pritchard, who, as manager of hardwood operations, also supervises the Voth operation. Mr. Pritchard's entire life has been spent in the hardwood industry.
Honey Island
About twenty miles out from Beaumont northwest on Highway number 69 the traveler comes upon Honey Island, Texas, where another mill of the Kirby group is located. The absence of both an island and bees first impresses the visitor, but the lumberman sees at once a sweet-running hive of industry busily turning out lumber at the rate of over 2,225,000 feet a month by means of a band mill and gang. Modern cross-circulation Moore dry kilns dry the entire production. Ample shed space, also of the Lamella type roof, keeps all lumber under roof so that from log pond, through cooling sheds and planing mill, not a board is exposed to the weather.
W. H. Bolton, the mill manager at Honey Island, while yet a comparatively young man, is a veteran in Kirby service and has run the gamut of practically every position in the lumber manufacturing business. He is also known to the retail trade in the Central Texas area where he sold Kirby lumber on the road years ago. Thus, there is embraced in this mill manager a rare combination of viewpoints of retailer, manufacturer, salesman and executive.
Kirby's Organization
The age-old question of "How many years can you run on your present supply of timber?" is not bothering Kirby. They're more concerned with the question, "Honest, is it as good as Kirby's?" their time-honored slogan, and they are doing everything they can to make that slogan more important and more challenging than ever before.
The same skill, craftsmanship, love of the job that the Kirby folks show at the mills, are also shown in the general offices. In the top floors of the Kirby Building, Houston, Messrs. H. M. Seaman, J. K. Herndon, and E. F. Horan, stand on the bridge of the good ship KIRBY.
Mr. Seaman is vice president and general manager. Mr. Herndon is sales manager in charge of pine. Mr. Horan is sales manager in charge of hardwood.
Their market extends to Mexico, Canada, England, South America, Europe, and throughout the United States. Aggressive in selling, modern in ideas, stable in their whole set-up, Kirby is one organization that does honor to Texas and to the lumber industry.
|
|
|
|
|
|
[top] |
|
|
|
|
 |
Text and images were digitized and proofread from the original source documents by Murry Hammond. Contact Murry for all corrections, additions, and contributions of new material. |
|
|
|